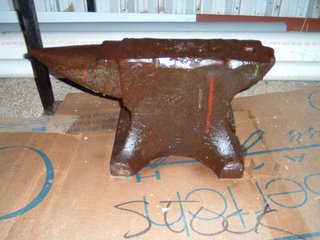
As you can see from this photo ... I have an anvil. I suspect that it is a cheaper anvil, but it does have a hardie hole. It is really chewed up, but it only cost me $10! I went over to a garage sale, and as soon as we walked up, the man said "You don't want an anvil, do you?" While we were there, he gave me a piece of shackle rod and a small barrel with re-bar legs that I might be able to add fire-brick and clay to make into a forge.
If you notice a shiny look to the anvil, it was a bit rusty, so I sprayed it down with penetrating oil. After I wipe the oil off, I'll look it over carefully, and decide whether I want to have it milled flat, or just to grind it smooth myself (much less accurate, but cheaper). The face is very scarred up, with chunks missing off of the heel, and a file says that it is at least medium hardness. I'm just hoping it is not an "Anvil Shaped Object". The only identifying marks on the anvil are "113" in raised letters on the waist, and possibly another inscription right above one of the feet. It has about a 7/8 inch hardie hole. and no pritchel hole (this was probably on the part of the heel that broke off). Also, below the hardie it has a large "12" in raised letters. The dimensions are 19.5 inches long x 9.5 inches high x 4.125 inches wide.
Update: I did a bounce test with a 2 lb hammer, but I couldn't reliably interpret the results. And if this anvil uses the English Hundredweight system, 113 = 1 * 112 + 1 * 28 + 3 * 1 = 143 pounds (minus material lost on the heel)! I am having some doubts about the barrel mini-forge ... I will have to discuss this one with some REAL blacksmiths.
1 comment:
Ran across your site, if this is too old a page then sorry, might help someone though.
Forget the hammer test. Try a ball bearing test: 1" ball bearing, 1' drop, measure height of rebound with a ruler and express as a percentage, average several tests in middle of face. Anvils that give +80% bounce are great to work on, anvils that give lower numbers are less great, cast iron objects give very little. Old anvils usually will do up to 75% or so, some are better. My 300# Hay-Budden does about 85% over its entire face, but they're considered "the Rolls-Royce of anvils" (Postman, Anvils in America) for a *reason*, and it wasn't $10 either, you got a great buy. You can use the bounce test for finding softer spots on used anvils too.
If I'm seeing the picture correctly the pritchel hole is still halfway there and may have started the crack that completely removed the heel. Pritchel holes are supposed to be used backup for through-punching and maybe a hold-down, that's it, sometimes fools drive heavy stock into them or do other dumb things, usually cold. Heavy work should be done in the middle of the face, quieter too. Deliberately smashing off the heel and/or cutting off the horn with heavy equipment was a way of decommissioning enemy anvils back through Civil War times too, horseshoes and blades being war materiel until quite recently.
I'm not good enough to ID your anvil from the info provided and many are pretty generic, Postman's book is a good source and several sites have some ID hints.
Never mill and don't grind until you know what you're doing, hardened face layers can be very thin in old anvils. Jock Dempsey has good restoration articles on anvilfire.com but remember that lots of good work has been done for centuries on random big hunks of steel or even stones back in Viking days. Rehardening a big anvil face can be done after welding up flaws but the quenching traditionally uses a diverted river and is not a one-person job.
Have fun with your anvil!
Grimbold, an old SCA smith
Post a Comment