Bill Kendall showed me a few of his hardie tools, and gave me a few ideas about how to make them from shackle rod aka "sucker rod" ends. He had a "hot cut", a bending fork, and a bick. He also showed me a piece of mild steel with a tab bent down that fits into the hardie to hold it in place.
I have one large piece of shackle rod, and a few smaller pieces, and I spotted a few rod pieces on a recent walk across my land. Since I don't want to use tongs, I am leaving the rod about 3 feet long.
First comment: wow! it takes some work to shape a 1.25 inch bar!
My recommended steps are: square up and draw down the shank to size (7/8 inch for me). Now form the chisel shape at end. A hot cutter has a thinner blade, while a cold cutter has a blunt "chisel shaped" working end. Now you can cut below the shank with a hacksaw, but make SURE you do not have any more forging to do. Try a little fine oil or cutting fluid. If the shank doesn't quite fit, you can file or grind it. I tried to heat and draw out my hardie shank that last 1/8 inch over the anvil, but I could not hold on to it with my tongs (I only have one pair that is remotely useful for that shape). I think the Uri Hofi Woop tongs demonstrated on IForgeIron might work. I have not tempered mine yet, but such a large chunk of metal would need a nice soak in the fire before quenching and tempering.
My adventures as a beginning blacksmith. Read about setting up my forge, finding and building tools, and making projects.
December 30, 2006
December 07, 2006
Cheap and Easy Brake Drum Forge
Here is a link to how to build a Brake Drum forge on the cheap. Personally, I would put the fire pot into a cut up 55 gallon drum to act as a wind shield and coal reservoir / pan, but he wanted to be able to break it down and store it compactly in his garage. My complements!
I am working on a freon can-based propane forge, with a "T-Jet" burner as recommended by Frosty on IForgeIron.com. I have gathered all of the parts, and will share the details after I have completed assembly and tested it out.
I am working on a freon can-based propane forge, with a "T-Jet" burner as recommended by Frosty on IForgeIron.com. I have gathered all of the parts, and will share the details after I have completed assembly and tested it out.
November 02, 2006
Bolt Tongs and Google Blacksmithing Videos
I worked on a pair of V-bit bolt tongs last weekend, but I did not finish them. They still need the boss (hinge area) flattened and drifted, and the handles need to be rounded and smoothed out. It is difficult but not impossible to draw out, straighten and flatten a piece of metal on a chewed up anvil. I think the hard top plate is simply missing on my anvil. After grinding on it some, I have a flat surface, and 2 inches of rounded edge suitable for drawing. All other edges are ragged or chipped. I need to learn how to arc weld, and lay down a new top with "hard-facing rod."
Making my tongs, I had to work out the process of forming the V bit. I flattened the bit from 1/2 or 5/8 inch round down to about a 1/4 inch thickness, then I put the bit in my swage block's smallest V shape and hit it with the pein end of my 2 pound cross pein hammer. Of course, all work was done hot, and the thinner metal lost heat very quickly since my swage was cool. A specialized tool like a smithing magician would be handy here. The critical part is getting the metal to fold at the center line. A smarter man would have taken some spare stock, heated and flattened it, and formed a few practice bits into V shape.
Below are some cool blacksmith videos found searching for blacksmith or forging:
Forging a nail - using a hammer, european style anvil and a header tool
Curl Making with the Anvil
Making a Katana from a railroad anchor (I think it is a clip):
Part 1, Part 2 and Part 3
Tempering tools, using a hot cut, a fancy twisted rod
Making my tongs, I had to work out the process of forming the V bit. I flattened the bit from 1/2 or 5/8 inch round down to about a 1/4 inch thickness, then I put the bit in my swage block's smallest V shape and hit it with the pein end of my 2 pound cross pein hammer. Of course, all work was done hot, and the thinner metal lost heat very quickly since my swage was cool. A specialized tool like a smithing magician would be handy here. The critical part is getting the metal to fold at the center line. A smarter man would have taken some spare stock, heated and flattened it, and formed a few practice bits into V shape.
Below are some cool blacksmith videos found searching for blacksmith or forging:
Forging a nail - using a hammer, european style anvil and a header tool
Curl Making with the Anvil
Making a Katana from a railroad anchor (I think it is a clip):
Part 1, Part 2 and Part 3
Tempering tools, using a hot cut, a fancy twisted rod
October 31, 2006
Propane Tank and LP Gas Forges
My apologies to those of you who read my posting on IForgeIron.com, as the first part of this post will be very familiar to you. Scroll down to see my thought on moving from "have tank" to "have propane forge". For those who have not been to IForgeIron, they have blueprints (step-by-step instructions and photos) of a few burners and gas forges.
My dad used to drive a propane truck, going to houses and filling their tanks. I told him once that I could use a propane tank, and he mentioned a 275 gallon tank on a trailer. That seemed a bit large to me, but then he remembered a smaller tank that came off of a tractor or a truck. It is a 43 gallon (358 pound) tank, with a gauge to see how full it is, valves for liquid, vapor, bleed off, vapor return, etc. And of course, a pop-off valve just in case someone fills it too full. This tank is heavy! I could lift one end, but we used a tractor's front end loader to load it into my truck.
I still need to get the gaskets inspected, get a cap for one of the return lines, paint it, and get it filled. After that, I will stop by my brothers to see if the hose, regulator and (hopefully) gauge from his old barbecue grill will be useful. I would prefer to have a "hard line" rather than hoses for my daily use forge, but I would also like to have a portable forge.
I would like to have two propane forges at the house. One of them should be a small, portable forge for demos, Saltfork Craftsmen's meetings, and going to a friends house (informal hammer-in's). I'm thinking about a freon tank forge here. The other should be larger, and capable of heating a car or truck coil spring for straightening. I would guess that would require a 12 or 14 inch diameter shell. So far, I am thinking of buying a pipe burner kit, some dura-wool and a small tub of "Plistix 900F" and making the freon forge. After I use that for a month or two, I will have a better idea about my needs. Maybe instead of making a large forge, I will get a T-Rex burner and make a brick-pile forge.
To satisfy your propane forge browsing needs, here are some links:
Zoeller forge price list
Rex Price's (T-Rex) Hybrid Burners
Chile Forge
Ellis Custom Knifeworks
Cashen Blades gas forge combustion processes
My dad used to drive a propane truck, going to houses and filling their tanks. I told him once that I could use a propane tank, and he mentioned a 275 gallon tank on a trailer. That seemed a bit large to me, but then he remembered a smaller tank that came off of a tractor or a truck. It is a 43 gallon (358 pound) tank, with a gauge to see how full it is, valves for liquid, vapor, bleed off, vapor return, etc. And of course, a pop-off valve just in case someone fills it too full. This tank is heavy! I could lift one end, but we used a tractor's front end loader to load it into my truck.
I still need to get the gaskets inspected, get a cap for one of the return lines, paint it, and get it filled. After that, I will stop by my brothers to see if the hose, regulator and (hopefully) gauge from his old barbecue grill will be useful. I would prefer to have a "hard line" rather than hoses for my daily use forge, but I would also like to have a portable forge.
I would like to have two propane forges at the house. One of them should be a small, portable forge for demos, Saltfork Craftsmen's meetings, and going to a friends house (informal hammer-in's). I'm thinking about a freon tank forge here. The other should be larger, and capable of heating a car or truck coil spring for straightening. I would guess that would require a 12 or 14 inch diameter shell. So far, I am thinking of buying a pipe burner kit, some dura-wool and a small tub of "Plistix 900F" and making the freon forge. After I use that for a month or two, I will have a better idea about my needs. Maybe instead of making a large forge, I will get a T-Rex burner and make a brick-pile forge.
To satisfy your propane forge browsing needs, here are some links:
Zoeller forge price list
Rex Price's (T-Rex) Hybrid Burners
Chile Forge
Ellis Custom Knifeworks
Cashen Blades gas forge combustion processes
October 24, 2006
Making tools to make hammers
A few weeks back, my blacksmith friend Tim mentioned that we should get together and make some handled tools - hammers, handled punches, fullers, etc. So last weekend, I went over to his shop, and we made a slitter and two hammer eye drifts. I brought some axles, leaf and coil springs and we picked an old 1 x 7/8 inch fixed axle to draw down for our drifts. We made them about 16 inches long, with the widest part at about 12 inches. We took turns on the 16 pound (7.25 kg) sledge hammer, and really moved the metal! We tried to keep our pieces straight as we forged, by doing some correcting blows, but there were still a few twists near the small end. Tim cleaned up one of the drifts with a flap sanding disk, and it looked beautiful. It needed a small amount of cleanup on the edges, but the overall shape was exactly what I was aiming for. We also straightened out a few coil springs using a bending fork mounted on a 4x4 inch piece of tubing set into a concrete pad with a 3 prong socket. The pair of heavy tongs that I had made came in very handy. Tim put a piece of square metal tubing over one end of the spring, and I held the other end with tongs, and we maneuvered the spring over to the bending forks. Then he would bend and I would position the spring for the next bend. After this, we ran out of time. At our next work session, we will smooth and straighten out the drifts, and hopefully make a few handled slitters or other small tools from our stash of car axle material. I think the axles and coil springs are 4140 material, but I am quite sure that they are steel!
Regarding the 16 pound sledge hammer, we didn't do the circular overhead swing, but rather a more controllable (and more tiring) swing where we lifted the head to eye level and then pushed or dropped it down. This was partly because I am not used to working with such a heavy hammer, and also because his anvil was only about 125 pound As I understand it, the recommended hammer to anvil ratio is between 1:15 and 1:25. With a 125 pound anvil, this works out to an eight pound (4 kg) hammer at most. Also, the anvil was mounted to a tree stump, and was 8 inches higher than I would like for sledge work.
I am sorry that I don't have pictures, but I will try to make up for it next time.
Regarding the 16 pound sledge hammer, we didn't do the circular overhead swing, but rather a more controllable (and more tiring) swing where we lifted the head to eye level and then pushed or dropped it down. This was partly because I am not used to working with such a heavy hammer, and also because his anvil was only about 125 pound As I understand it, the recommended hammer to anvil ratio is between 1:15 and 1:25. With a 125 pound anvil, this works out to an eight pound (4 kg) hammer at most. Also, the anvil was mounted to a tree stump, and was 8 inches higher than I would like for sledge work.
I am sorry that I don't have pictures, but I will try to make up for it next time.
October 18, 2006
2006 Saltfork Conference
Another member of our group, Tim, kindly invited me to go with him to the SCABA Annual Conference in Perry, Oklahoma. We had demonstrations by Tal Harris, and the Brazil brothers - Brian and Ed. The building was excellent, with bleachers close to the demonstrators, a separating wall to isolate sound and sand on the floor so we would not have to worry about fires. To all SCABA members - there should be a tape available early next year.
Tal showed us how to design a railing with pierced joinery, tenons and banding. He used a few specialized tools that he either made or adapted for his purposes - a 6 inch traveler, a bolster block with a slit cut, a Z shaped auto-centering scoring tool, an offset punch, an angle iron measuring stick (with small clamps to preserve a measure across several cuts), a ruler that measures length on one side and the radius on the other. He commented - if you look at an older piece and it looks impossible, there was probably a forge weld involved. His design explanations only involved simple math, using the perimeter, circumference and area formulas as he converted a slit into a circle and then a square.
Brian and Ed demonstrated tool making, animal heads, an eagle wing, and several flowers. They used both a traditional "London Pattern" anvil as well as a european anvil made more like a simplified swage block - it was a piece of 2.5 or 3 inch plate, turned on edge, with flat, 2 inch rounded fuller, 1/2 inch fuller, cutting edge, hardy hole, pritchel hole and a small horn.
Things that I learned:
An offset punch allows access to the inside of a closed shape.
Measure carefully.
Marking with a diamond punch makes it easier to spot a mark after the metal has scale.
Scale will flake off when an item has been upset some.
Quenching a piece can shrink it a tiny bit (maybe 1/16 inch over 6 inches).
You can draw out faster if you slightly lift the hot piece off of the anvil between blows, thus preserving the heat.
Tal showed us how to design a railing with pierced joinery, tenons and banding. He used a few specialized tools that he either made or adapted for his purposes - a 6 inch traveler, a bolster block with a slit cut, a Z shaped auto-centering scoring tool, an offset punch, an angle iron measuring stick (with small clamps to preserve a measure across several cuts), a ruler that measures length on one side and the radius on the other. He commented - if you look at an older piece and it looks impossible, there was probably a forge weld involved. His design explanations only involved simple math, using the perimeter, circumference and area formulas as he converted a slit into a circle and then a square.
Brian and Ed demonstrated tool making, animal heads, an eagle wing, and several flowers. They used both a traditional "London Pattern" anvil as well as a european anvil made more like a simplified swage block - it was a piece of 2.5 or 3 inch plate, turned on edge, with flat, 2 inch rounded fuller, 1/2 inch fuller, cutting edge, hardy hole, pritchel hole and a small horn.
Things that I learned:
An offset punch allows access to the inside of a closed shape.
Measure carefully.
Marking with a diamond punch makes it easier to spot a mark after the metal has scale.
Scale will flake off when an item has been upset some.
Quenching a piece can shrink it a tiny bit (maybe 1/16 inch over 6 inches).
You can draw out faster if you slightly lift the hot piece off of the anvil between blows, thus preserving the heat.
October 03, 2006
What is in a clothes dryer?
Recently, I acquired 2 washers and 2 dryers. After dismantling my first dryer, I was somewhat surprised at how simply they are made. The frame was nothing more than the painted sheet steel box that you see from the outside. Inside was a single sheet running top to bottom acting as a drum support and motor mount.
From the first drier, we have:
It looks like we have parts for a coal forge: sheet for the "table" area, as well as the obvious blower. I bought a varistor at a garage sale, rated for 5 amps. I wonder if I could mount the varistor in line with the blower, and not use an air gate?
I was pleased to discover that the blower motor (which also spins the clothes drum) was 110 volts. The dryer was a 220 volt unit (two 110 volt lines, and a neutral) but I guess one "leg" ran the blower, and the other "leg" operated the heater. My primary reason for obtaining these units was to gather parts for a power hammer, although Jim C had a forge blower blueprint using a dryer fan on IForgeIron.com, so I wanted to try that out too.
From the first drier, we have:
- 1/3 hp open-frame 110 volt motor, rated for 5.8 amps
- sheet metal blower housing
- lots of flat sheet metal.
It looks like we have parts for a coal forge: sheet for the "table" area, as well as the obvious blower. I bought a varistor at a garage sale, rated for 5 amps. I wonder if I could mount the varistor in line with the blower, and not use an air gate?
I was pleased to discover that the blower motor (which also spins the clothes drum) was 110 volts. The dryer was a 220 volt unit (two 110 volt lines, and a neutral) but I guess one "leg" ran the blower, and the other "leg" operated the heater. My primary reason for obtaining these units was to gather parts for a power hammer, although Jim C had a forge blower blueprint using a dryer fan on IForgeIron.com, so I wanted to try that out too.
Quest for Power - Gathering Supplies
After the September 2006 SCABA Meeting at Dan's house, I have been wanting a power hammer. So I have been scouring the internet, looking at pictures, plans and opinions. So now I have to decide whether to build an Appalachian Power Hammer, a Little Giant knockoff or a Kinyon style air hammer. So far, Rusty is winning the battle, with potential out-of-pocket expenses of $200 US dollars or less, but the simplicity of an air hammer has its charm too. Maybe I will build an air hammer someday when I have $1000 US dollars or so for the huge air compressor, air cylinder and fittings. Actually, there is a very informative thread on IForgeIron.com regarding hammer weight and cylinder dimensions for Kinyon style hammers. It seems like I might be able to get by with less than $1000 if I only want a 20 or 30 pound hammer. If I had alot of money, I would just get a Phoenix Air Hammer and get back to forging.
While I really want a power hammer, I also want to keep learning hammer control and basic "At The Anvil" blacksmithing. I don't want to become so dependent on power tools and dies that I can't work without them!
So far, I have the following:
I intend to scrounge a 1/2 HP electric motor from one of my washers (110 volt) or dryers (220 volt). Obviously the washer is preferred, unless the dryer has a universal motor that can be run at a lower speed on 110 volts. That would be awesome, since I don't need more than 100 beats per minute. I've read that 220 volt motors are more efficient. Maybe I just need to get my shop wired for 220.
Links mentioned or reviewed while creating this article are:
http://www.anvilfire.com/power/index.htm
http://www.appaltree.net/rusty/
http://www.metalwebnews.com/howto/hammer/hammer.html
http://www.iforgeiron.com
http://www.geocities.com/zoellerforge/hammer.html
http://www.metalsmithinghowto.com/content/AirHammer/Rosche/air_hammer.html
http://magichammer.freeservers.com/page2.html
http://www.phoenixhammer.com/
While I really want a power hammer, I also want to keep learning hammer control and basic "At The Anvil" blacksmithing. I don't want to become so dependent on power tools and dies that I can't work without them!
So far, I have the following:
- a set of trailer overload leaf springs
- a few broken pieces of leaf spring
- several car and truck coil springs
- three car axles
- one 12 in x 48 in x 1 in thick plate
- one 9 in x 32+ in x 2 in thick plate
- two junk washers and two driers
- access to some rusty old farm equipment
- ... and determination
I intend to scrounge a 1/2 HP electric motor from one of my washers (110 volt) or dryers (220 volt). Obviously the washer is preferred, unless the dryer has a universal motor that can be run at a lower speed on 110 volts. That would be awesome, since I don't need more than 100 beats per minute. I've read that 220 volt motors are more efficient. Maybe I just need to get my shop wired for 220.
Links mentioned or reviewed while creating this article are:
http://www.anvilfire.com/power/index.htm
http://www.appaltree.net/rusty/
http://www.metalwebnews.com/howto/hammer/hammer.html
http://www.iforgeiron.com
http://www.geocities.com/zoellerforge/hammer.html
http://www.metalsmithinghowto.com/content/AirHammer/Rosche/air_hammer.html
http://magichammer.freeservers.com/page2.html
http://www.phoenixhammer.com/
September 17, 2006
Good tongs
Ok, so my first pair of tongs aren't good ... but they work. I made some "practice" tongs out of shackle rod. It seems that shackle rod is workable, and not pressed scrap metal like concrete re-inforcement bar (re-bar). I used an article from anvilfire.com called simply Tongs. The reins, hinge and jaws are all a bit rough, but I am pleased with them as a first effort. I took them to the September 2006 Saltfork Blacksmith meeting, and reworked the reins and jaws using a power hammer. After making these, I learned 2 lessons: start shaping a round or v bit early on, and don't be in too much of a hurry riveting them together. After they cool down, you will see square corners that need rounding, etc.
A quick note on this picture. I was wearing gloves because I was wire-brushing my tong to clean off scale. If I am forging, I use 1 glove on the tong hand at most.
A few months back, my dad gave me an old Sears 1/4 hp grinder with a wire brush. I bought a grinder stand at Harbor Freight. Over the labor day weekend, I drilled 4 mounting holes and mounted it up. After donning an apron, gloves and a full face shield, I wire brushed an old rusted hammer head that I found behind my parents' house. It looked so much better that I wire brushed my tongs too!
A blacksmith told me that shackle rod should probably not be hardened, as it gets quite brittle in a water quench. I know this is true for re-bar, but shackle rod does not feel as hard to me.
Below are some collected bits of wisdom:
From "Forge & Anvil": Good tongs have a solid hinge.
From "Practical Blacksmithing": Good jaws are set so they touch at the tip first, and grab completely as you squeeze.
From IForgeIron: A refinement to Riveting your tongs.
Uri Hofi punches and drifts his hinges. This probably allows for a wider range of motion, and a smoother joint.
Ideally, tongs should have an offset in the handle right by the joint that allows them to hang over a 3/8 or 1/2 in bar without the handles spread out. This makes for a neat and tidy shop, and saves space.
A quick note on this picture. I was wearing gloves because I was wire-brushing my tong to clean off scale. If I am forging, I use 1 glove on the tong hand at most.
A few months back, my dad gave me an old Sears 1/4 hp grinder with a wire brush. I bought a grinder stand at Harbor Freight. Over the labor day weekend, I drilled 4 mounting holes and mounted it up. After donning an apron, gloves and a full face shield, I wire brushed an old rusted hammer head that I found behind my parents' house. It looked so much better that I wire brushed my tongs too!
A blacksmith told me that shackle rod should probably not be hardened, as it gets quite brittle in a water quench. I know this is true for re-bar, but shackle rod does not feel as hard to me.
Below are some collected bits of wisdom:
From "Forge & Anvil": Good tongs have a solid hinge.
From "Practical Blacksmithing": Good jaws are set so they touch at the tip first, and grab completely as you squeeze.
From IForgeIron: A refinement to Riveting your tongs.
Uri Hofi punches and drifts his hinges. This probably allows for a wider range of motion, and a smoother joint.
Ideally, tongs should have an offset in the handle right by the joint that allows them to hang over a 3/8 or 1/2 in bar without the handles spread out. This makes for a neat and tidy shop, and saves space.
September 11, 2006
September 2006 Saltfork Craftsmens Meeting
The Saltfork Craftsmen Artist Blacksmith Association held another blacksmith's meeting at Dan Cowart's shop. If you live in the Bartlesville or Dewey area, you missed out! I forgot my camera, so please accept my apology for not taking pictures. We had 4 beginners there (counting me) and about 14 total attending. I brought a pair of heavy tongs that I had rough-forged from 5/8" shackle rod. Some of the more experienced blacksmiths advised me to draw out the handles more and draw out the bit more too. So, I chiseled off the old home-made rivet and took advantage of the opportunity to use Dan's power hammer to draw out the reins. Wow! I want a power hammer! After re-riveting the tongs, I tried to form a V in the bit. I think that was a mistake. Also, I should have spent a bit more time thinking about that problem - I ended up using the edge where the top plate meets the horn to hold the bits steady and chiseling a small line down the middle, but I couldnt get them to fold into a V - they just wanted to twist. That was a good lesson for me - don't get in a hurry, and think through all of the steps you will be taking. A while later, I remembered the swage block, but I will have to try that at home. After the meeting, I went to a garage sale and found a beat-up 1/4" top fuller without handle, a few ball pein hammers and some older wooden handles. That fuller plus the V edge of my swage block might just do it.
Another thing I did at the meeting was to start on a blunt punch from a car coil spring (probably 4140).
That night, I was looking at power hammer plans (I don't want to spend alot of money on one - this is a hobby). The appalachian power hammer page looks very interesting, and it looks affordable. It looks like I can make between a 15 and 25 pound hammer for less than $200 USD. I already have some trailer over-load leaf springs, a lead on some washer and dryer motors and a source for some of the metal.
I will more blog about the power hammer after I have collected enough scrap to get started.
Some other power hammer links are below
AnvilFire's coverage of a Junk Yard Hammer
I Forge Iron - Power Hammer by Jeff Reinhardt
I will add several more links tonight.
If you are wondering what we do, look in the archives for my blog of the January 2006 and March 2006 meetings.
[edit: added meeting notes]
Another thing I did at the meeting was to start on a blunt punch from a car coil spring (probably 4140).
That night, I was looking at power hammer plans (I don't want to spend alot of money on one - this is a hobby). The appalachian power hammer page looks very interesting, and it looks affordable. It looks like I can make between a 15 and 25 pound hammer for less than $200 USD. I already have some trailer over-load leaf springs, a lead on some washer and dryer motors and a source for some of the metal.
I will more blog about the power hammer after I have collected enough scrap to get started.
Some other power hammer links are below
AnvilFire's coverage of a Junk Yard Hammer
I Forge Iron - Power Hammer by Jeff Reinhardt
I will add several more links tonight.
If you are wondering what we do, look in the archives for my blog of the January 2006 and March 2006 meetings.
[edit: added meeting notes]
August 30, 2006
Other Blacksmith Blogs and Links
Recently, I have read a book "Metallurgy fundamentals" by Daniel A Brandt. It is written in the style of a 7th grade physical science book - definitely an introductory text. I am glad to learn about the various crystals: ferrite, pearlite, cementite, the molten austenite, and the hardened form - martensite. I have not run across "Isothermal Transformation Diagrams" more than maybe once before, and I'm not sure why I don't see alot of them in blacksmithing books. I would guess that most blacksmiths use the metal color and personal judgement as their guide.
I am still working at the craft, but until I have a more respectable update, here are some links.
Google Books - Blacksmith has some older books with full text. I believe they will be allowing PDF download soon.
Steel Working and Tool Dressing: A Manual of Practical Information for Blacksmiths and All Other Workers in Steel and Iron
The Modern Practice of American Machinists & Engineers: Including the Construction, Application,...
George Dixon - creator of Artist-Blacksmith Magazine
http://artist-blacksmith.blogspot.com
Yet Another Railroad Track Anvil Project
http://www.castle-ranch.com/crafts/Anvil/anvil.htm
(has a recipe for cutting oil)
From The Blacksmith's Corner
http://blacksmithscorner.blogspot.com/
Free PDF Craft Books - some of these are EXCELLENT!
http://www.countryside.gov.uk/NewEnterprise/Economies/craftpublications.asp
Mechanical Engineer's Handbook, 1916 edition
http://chla.library.cornell.edu
Good Books from Amazon
edit: removed a dead link.
I am still working at the craft, but until I have a more respectable update, here are some links.
Google Books - Blacksmith has some older books with full text. I believe they will be allowing PDF download soon.
Steel Working and Tool Dressing: A Manual of Practical Information for Blacksmiths and All Other Workers in Steel and Iron
The Modern Practice of American Machinists & Engineers: Including the Construction, Application,...
George Dixon - creator of Artist-Blacksmith Magazine
http://artist-blacksmith.blogspot.com
Yet Another Railroad Track Anvil Project
http://www.castle-ranch.com/crafts/Anvil/anvil.htm
(has a recipe for cutting oil)
From The Blacksmith's Corner
http://blacksmithscorner.blogspot.com/
Free PDF Craft Books - some of these are EXCELLENT!
http://www.countryside.gov.uk/NewEnterprise/Economies/craftpublications.asp
Mechanical Engineer's Handbook, 1916 edition
http://chla.library.cornell.edu
Good Books from Amazon
edit: removed a dead link.
July 20, 2006
Lessons for July 2006
Well, I've had a chance to heat up the forge this month - working on a hardie tool, my first pair of tongs, and straightening a car spring so I can use it as tool stock. As such, I have learned a few lessons useful to beginners. Keep in mind that I'm using hardwood charcoal right now, not coal. Charcoal seems to spark up alot, especially if it is a bit damp. Also, it doesn't seem to get as hot as coal. My metal turns to red or orange, but not to pale yellow or white.

I find that ripped and balled up newspaper with a few small twigs on top starts my fire quickly. Since I have a hand-crank forge, I give the kindling a gentle breeze to encourage it. It is best to forge in a long sleeved cotton shirt, a leather apron, and solid shoes that can't catch an errant spark.
Also, I just bought "New Edge of the Anvil" by Jack Andrews. So far, I am enjoying reading about the basic processes. I like the fact that he doesn't seem to leave any steps out. He starts with an overview of the equipment needed, as well as equipment that will be obtained in the future; then he starts the "working" part of the book with lighting a fire.
After I have built my first set of tongs, I will try to do a step-by-step when I make my next pair. I used the iForge tongs article on AnvilFire.

I find that ripped and balled up newspaper with a few small twigs on top starts my fire quickly. Since I have a hand-crank forge, I give the kindling a gentle breeze to encourage it. It is best to forge in a long sleeved cotton shirt, a leather apron, and solid shoes that can't catch an errant spark.
Also, I just bought "New Edge of the Anvil" by Jack Andrews. So far, I am enjoying reading about the basic processes. I like the fact that he doesn't seem to leave any steps out. He starts with an overview of the equipment needed, as well as equipment that will be obtained in the future; then he starts the "working" part of the book with lighting a fire.
After I have built my first set of tongs, I will try to do a step-by-step when I make my next pair. I used the iForge tongs article on AnvilFire.
May 08, 2006
Charcoal making
First ... why don't I just buy some charcoal at the local store? Well, most of this is in a pressed brick form, and is not pure wood product. It is too dirty to use in a forge (among other things). If you are careful, you can get real wood charcoal for about $5.00 per bag at Walmart. This is what I have been using recently, but I live on 20 acres of land in the country, and I would like to be a bit more self-sufficient. I collected the following links, but have not been able to try them out due to a burn ban in Oklahoma. The burn ban was recently lifted, so maybe I can give one of the simpler methods a try.
Here are the links and ideas about charcoal making that I have found recently.
Discovery has a good educational article on charcoal's benefits
Backwoods Home: Makeshift Forge and simple directions for Charcoal
Making charcoal in a 55 gallon drum.
Making charcoal by re-directing the volatiles down into the fire.
BBQ Charcoal Making
Arkansas Charcoal
If someone tries this out, be sure to take pictures and share your blog link, or just add a comment here.
Here are the links and ideas about charcoal making that I have found recently.
Discovery has a good educational article on charcoal's benefits
Backwoods Home: Makeshift Forge and simple directions for Charcoal
Making charcoal in a 55 gallon drum.
Making charcoal by re-directing the volatiles down into the fire.
BBQ Charcoal Making
Arkansas Charcoal
If someone tries this out, be sure to take pictures and share your blog link, or just add a comment here.
March 28, 2006
March 2006 Saltfork Craftsmens Meeting
I attended the March 2006 North-East regional meeting of the Saltfork Craftsmen Artist-Blacksmith Association at Dan and Pat Cowart's house. It was a fairly casual affair. Mike Sweeney brought a chunk of exotic metal and forged a rough knife blade using Dan's power hammer. After this, Mike and Mike made a scrolling tool but they were not especially hapy with it. Jim Caruthers made 2 napkin rings and gave them to Pat Cowart. Jim Caruthers then made a bottle opener, and even added a collar with help from Ed Brazeal. Ed made a collaring tool right there on the spot! Jim Caruthers took some time towards the end of the meeting to give a lesson to a college student and I. We made a J hook that you nail into the wall to hang a hat or coat on. Tracy (Dan's son) stood by and helped me through the project.
After it was all over, Dan loaned me a portable hand-crank coal forge! Look for more about that in my next blog.
Here are the pictures:
After it was all over, Dan loaned me a portable hand-crank coal forge! Look for more about that in my next blog.
Here are the pictures:
February 01, 2006
Looking for a Forge
I need a forge, be it coal, propane, natural gas - whatever! Since I am trying to get started "on a shoe-string," I will probably have to make a coal forge from the scrap that I am selectively gathering. As a side note, I try very hard not to take home something that I can't use. When I ran across some 3 to 4 foot long 2x4 lumber, I asked around work and gave about 18 sticks away to a friend who was renovating their house. I don't want to be wasteful, but I also don't want to fill my shop with so much stuff that I can't do any work.
Anyone who has read my earlier posts knows that I have been scrounging. That is a good thing, as alot of this stuff would be thrown away, and contributing to the landfills of our consumption-based materialistic society - don't get me started. My brother tipped me off to my latest "find" - a business had closed down, and they were renovating the insides. Actually, they were gutting the shelves and display areas. My brother received permission to take all he wanted: a wire security cage, plywood, 2x4, pressed board shelving, metal shelf arms and wall strips, wall-mounted electrical strips, 2 outlet electrical boxes and laminated shelves. We had to pull the stuff over one weekend, since the wrecking crew were coming monday, and they would be smashing instead of pulling every screw and nail. We probably pulled 40+ 2x4s, 120+ shelf brackets, 6 electrical strips, 12+ electrical boxes and a few pressed board shelves. That is cool and all, but none of this really contributed to my immediate forging goals.
I found some square tubing and angle iron (in the form of a shed door) in the brush behind my house (I haven't had time to clean up my land yet.) I'm thinking about cutting it up to make legs for a coal forge, or maybe a work bench.
I will probably not build a concrete block and brick forge - just too bulky. I might make a brake drum forge, or just use the plans from "Forge & Anvil" - a wheelbarrow pan with fire brick, fire clay and a wooden frame. I have some 2x4 wood scraps that would work fine, but no fire brick or fire clay. Lowes has a tiny plastic container of fireplace repair mortar - maybe 8 ounces. Any kind of coal forge will need a firepot, a tuyere, and a blower. The blower might end up costing me a few dollars if I have to buy it off of ebay. I am hoping to use some pipe and a home-made grate to make a poor-man's tuyere. I would love to find some 10 to 12 inch stove pipe so I could position the forge inside my shop, rather than at the door.
In other news, I have been looking for charcoal making instructions on the web. I'll share my findings with you in a future entry.
IForgeIron.com had a tip: Flexible metal dryer vent can be used for the air supply connection to the forge. We'll see.
A fellow member of SCABA is going to loan me a coal forge for a few months! Now all I have to do is go visit him.
Update: A mechanic friend mentioned that I should be VERY careful with brake drums, since brake pads may have asbestos in them, and the asbestos embeds itself into the drum. Let's hope you find a drum with Kevlar pads. I don't have specific safety recommendations for you, but use a tight-sealing air mask when handling and cleaning your brake drum!
Anyone who has read my earlier posts knows that I have been scrounging. That is a good thing, as alot of this stuff would be thrown away, and contributing to the landfills of our consumption-based materialistic society - don't get me started. My brother tipped me off to my latest "find" - a business had closed down, and they were renovating the insides. Actually, they were gutting the shelves and display areas. My brother received permission to take all he wanted: a wire security cage, plywood, 2x4, pressed board shelving, metal shelf arms and wall strips, wall-mounted electrical strips, 2 outlet electrical boxes and laminated shelves. We had to pull the stuff over one weekend, since the wrecking crew were coming monday, and they would be smashing instead of pulling every screw and nail. We probably pulled 40+ 2x4s, 120+ shelf brackets, 6 electrical strips, 12+ electrical boxes and a few pressed board shelves. That is cool and all, but none of this really contributed to my immediate forging goals.
I found some square tubing and angle iron (in the form of a shed door) in the brush behind my house (I haven't had time to clean up my land yet.) I'm thinking about cutting it up to make legs for a coal forge, or maybe a work bench.
I will probably not build a concrete block and brick forge - just too bulky. I might make a brake drum forge, or just use the plans from "Forge & Anvil" - a wheelbarrow pan with fire brick, fire clay and a wooden frame. I have some 2x4 wood scraps that would work fine, but no fire brick or fire clay. Lowes has a tiny plastic container of fireplace repair mortar - maybe 8 ounces. Any kind of coal forge will need a firepot, a tuyere, and a blower. The blower might end up costing me a few dollars if I have to buy it off of ebay. I am hoping to use some pipe and a home-made grate to make a poor-man's tuyere. I would love to find some 10 to 12 inch stove pipe so I could position the forge inside my shop, rather than at the door.
In other news, I have been looking for charcoal making instructions on the web. I'll share my findings with you in a future entry.
IForgeIron.com had a tip: Flexible metal dryer vent can be used for the air supply connection to the forge. We'll see.
A fellow member of SCABA is going to loan me a coal forge for a few months! Now all I have to do is go visit him.
Update: A mechanic friend mentioned that I should be VERY careful with brake drums, since brake pads may have asbestos in them, and the asbestos embeds itself into the drum. Let's hope you find a drum with Kevlar pads. I don't have specific safety recommendations for you, but use a tight-sealing air mask when handling and cleaning your brake drum!
January 19, 2006
A wooden anvil stand
I need a stand for my anvil. I spotted a simple stand at the January 2006 Saltfork Craftsmen's meeting that I think I could build.
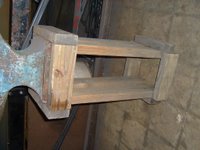
I modified the design to fit the miscellaneous lumber that I have available. I used:
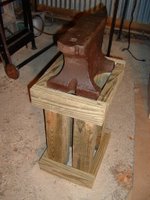
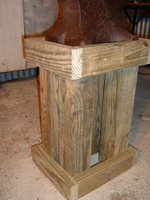
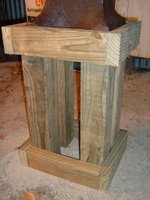
Since I used 4x4 supports, I haven't added any metal strapping or cross-bracing to this. I am not sure if I want to use the same stand for both anvil and swage block, or to make another one to support my swage block. The anvil base measures 9.25 x 11 inches, and the swage block measures 12 x 7.5 x 3.5 inches. Since I have limited floor space, I might end up using the swage block in the same stand. For that purpose, I made the stand hold a 12 x 9.5 inch tool. If you want to make one, measure from the floor to your knuckles, add 2 inches to avoid hyper-extension of your elbow joint, and subtract the height of your anvil. This is the height of your uprights (22 inches in my case). You can make the sides about 1/2 inch longer than the length of your anvil/swage base. For the ends you should add 1/2 inch for slop and 3 1/4 inches to overlap the two "side" 2x4s.
Regarding the anvil, I have worked the top and sides with a wire-brush to remove some of the rust and paint. I haven't taken a grinder to it yet, as I'm not sure if that is wise. I can take metal off quickly, but putting it back on would be very difficult.
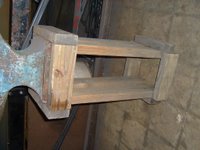
I modified the design to fit the miscellaneous lumber that I have available. I used:
- four 2x4 boards 12 1/2 inches for sides (these boards are flush with the uprights)
- four 2x4 boards 12 3/8 inches for ends (these boards overlap the ends of the other 2x4s)
- four 4x4 boards 22 inches for uprights
- 3 1/2 inch screws
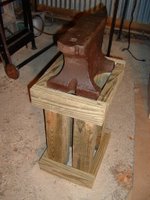
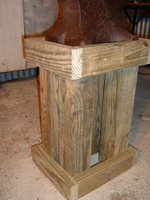
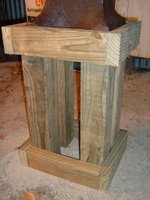
Since I used 4x4 supports, I haven't added any metal strapping or cross-bracing to this. I am not sure if I want to use the same stand for both anvil and swage block, or to make another one to support my swage block. The anvil base measures 9.25 x 11 inches, and the swage block measures 12 x 7.5 x 3.5 inches. Since I have limited floor space, I might end up using the swage block in the same stand. For that purpose, I made the stand hold a 12 x 9.5 inch tool. If you want to make one, measure from the floor to your knuckles, add 2 inches to avoid hyper-extension of your elbow joint, and subtract the height of your anvil. This is the height of your uprights (22 inches in my case). You can make the sides about 1/2 inch longer than the length of your anvil/swage base. For the ends you should add 1/2 inch for slop and 3 1/4 inches to overlap the two "side" 2x4s.
Regarding the anvil, I have worked the top and sides with a wire-brush to remove some of the rust and paint. I haven't taken a grinder to it yet, as I'm not sure if that is wise. I can take metal off quickly, but putting it back on would be very difficult.
Subscribe to:
Posts (Atom)