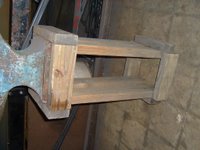
I modified the design to fit the miscellaneous lumber that I have available. I used:
- four 2x4 boards 12 1/2 inches for sides (these boards are flush with the uprights)
- four 2x4 boards 12 3/8 inches for ends (these boards overlap the ends of the other 2x4s)
- four 4x4 boards 22 inches for uprights
- 3 1/2 inch screws
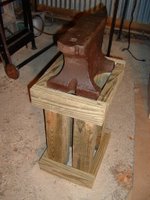
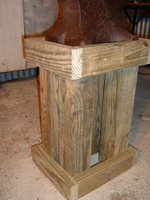
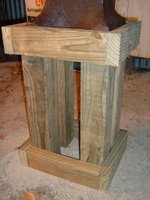
Since I used 4x4 supports, I haven't added any metal strapping or cross-bracing to this. I am not sure if I want to use the same stand for both anvil and swage block, or to make another one to support my swage block. The anvil base measures 9.25 x 11 inches, and the swage block measures 12 x 7.5 x 3.5 inches. Since I have limited floor space, I might end up using the swage block in the same stand. For that purpose, I made the stand hold a 12 x 9.5 inch tool. If you want to make one, measure from the floor to your knuckles, add 2 inches to avoid hyper-extension of your elbow joint, and subtract the height of your anvil. This is the height of your uprights (22 inches in my case). You can make the sides about 1/2 inch longer than the length of your anvil/swage base. For the ends you should add 1/2 inch for slop and 3 1/4 inches to overlap the two "side" 2x4s.
Regarding the anvil, I have worked the top and sides with a wire-brush to remove some of the rust and paint. I haven't taken a grinder to it yet, as I'm not sure if that is wise. I can take metal off quickly, but putting it back on would be very difficult.